Destylacja rozpuszczalników to proces, który ma na celu oddzielenie składników mieszaniny na podstawie różnicy w ich temperaturach wrzenia. W praktyce polega to na podgrzewaniu cieczy do momentu, gdy jeden z jej składników zaczyna parować. Para ta jest następnie schładzana i kondensowana, co pozwala na uzyskanie czystego rozpuszczalnika. Proces ten jest szeroko stosowany w przemyśle chemicznym, farmaceutycznym oraz w laboratoriach badawczych. W przypadku destylacji prostych rozpuszczalników, takich jak woda czy etanol, można wykorzystać standardowe aparaty destylacyjne, które składają się z kolby grzewczej, chłodnicy i naczynia odbierającego. Ważne jest, aby kontrolować temperaturę podczas destylacji, ponieważ zbyt wysoka temperatura może prowadzić do niepożądanych reakcji chemicznych. Dodatkowo, w przypadku mieszanin o bliskich temperaturach wrzenia, konieczne może być zastosowanie destylacji frakcyjnej, która pozwala na bardziej precyzyjne oddzielenie składników poprzez wielokrotne skraplanie i parowanie.
Jakie są zalety i wady destylacji rozpuszczalników
Destylacja rozpuszczalników ma wiele zalet, które sprawiają, że jest to jedna z najczęściej stosowanych metod separacji w przemyśle i laboratoriach. Przede wszystkim jest to metoda skuteczna i relatywnie prosta do przeprowadzenia. Dzięki niej można uzyskać wysokiej czystości produkty, co jest kluczowe w wielu zastosowaniach przemysłowych oraz badawczych. Ponadto proces ten jest dobrze znany i opisany w literaturze naukowej, co ułatwia jego wdrożenie oraz optymalizację. Jednakże istnieją również pewne wady związane z destylacją rozpuszczalników. Po pierwsze, proces ten może być energochłonny, zwłaszcza w przypadku substancji o wysokich temperaturach wrzenia. Wymaga to dużych nakładów energii oraz odpowiednich urządzeń grzewczych. Dodatkowo, destylacja nie zawsze jest skuteczna w przypadku mieszanin o bardzo bliskich temperaturach wrzenia, co może prowadzić do niepełnej separacji składników.
Jakie są zastosowania destylacji rozpuszczalników w przemyśle
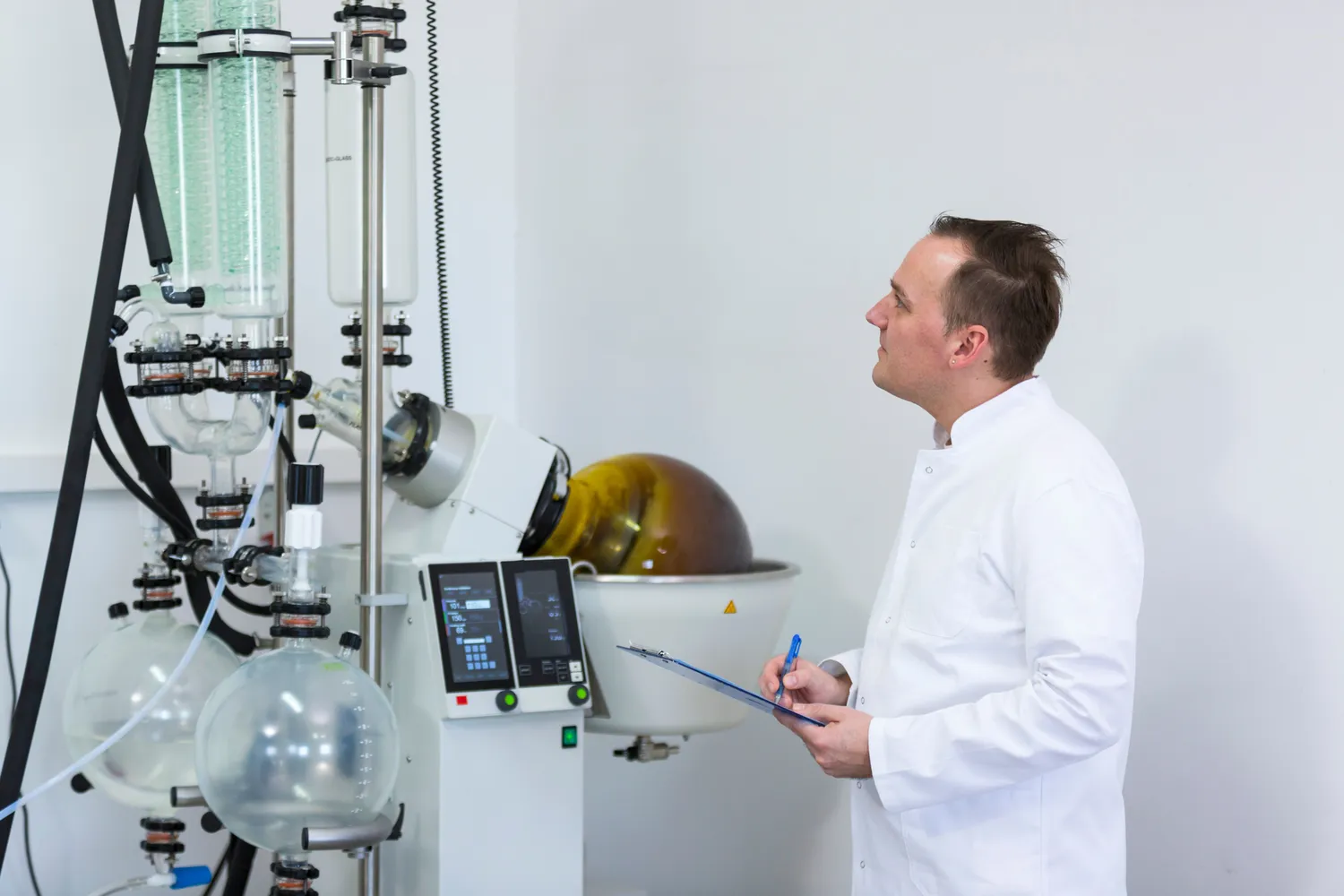
Destylacja rozpuszczalników znajduje szerokie zastosowanie w różnych branżach przemysłowych. W przemyśle chemicznym jest wykorzystywana do oczyszczania surowców oraz produktów końcowych. Na przykład etanol produkowany z fermentacji może być poddany destylacji w celu usunięcia zanieczyszczeń oraz uzyskania wyższej czystości produktu. W przemyśle farmaceutycznym destylacja odgrywa kluczową rolę w produkcji leków oraz substancji czynnych. Dzięki temu możliwe jest uzyskanie preparatów o wysokiej jakości i czystości, co jest niezbędne dla bezpieczeństwa pacjentów. Ponadto destylacja jest często stosowana w produkcji alkoholi oraz napojów spirytusowych, gdzie celem jest uzyskanie pożądanej mocy trunku oraz aromatu. W laboratoriach badawczych natomiast destylacja służy do analizy składników mieszanin oraz do przygotowywania prób do dalszych badań.
Jakie są różnice między różnymi metodami destylacji rozpuszczalników
W kontekście destylacji rozpuszczalników istnieje kilka różnych metod, które różnią się od siebie zarówno zasadą działania, jak i zastosowaniem. Najbardziej podstawową formą jest destylacja prosta, która polega na jednorazowym podgrzewaniu cieczy i zbieraniu pary skondensowanej. Jest to metoda stosunkowo łatwa do przeprowadzenia, ale jej skuteczność ogranicza się do mieszanin o wyraźnie różniących się temperaturach wrzenia. Z kolei destylacja frakcyjna to bardziej zaawansowana technika, która umożliwia oddzielanie składników o bliskich temperaturach wrzenia poprzez wielokrotne skraplanie i parowanie w kolumnie frakcyjnej. Ta metoda zapewnia znacznie wyższą efektywność separacji i jest powszechnie stosowana tam, gdzie wymagana jest wysoka czystość produktu końcowego. Inną metodą jest destylacja azeotropowa, która wykorzystuje dodatki chemiczne do zmiany właściwości mieszaniny i umożliwienia separacji składników tworzących azeotrop.
Jakie są najczęstsze błędy podczas destylacji rozpuszczalników
Podczas przeprowadzania procesu destylacji rozpuszczalników, istnieje wiele pułapek, które mogą prowadzić do nieefektywności lub wręcz niepowodzenia całej operacji. Jednym z najczęstszych błędów jest niewłaściwe ustawienie temperatury. Zbyt wysoka temperatura może powodować niepożądane reakcje chemiczne, a także prowadzić do przegrzania sprzętu. Z drugiej strony, zbyt niska temperatura może skutkować niedostatecznym odparowaniem składników, co ogranicza efektywność separacji. Kolejnym istotnym błędem jest niewłaściwe dobranie aparatury destylacyjnej do rodzaju mieszaniny. Użycie kolby destylacyjnej zamiast kolumny frakcyjnej w przypadku mieszanin o bliskich temperaturach wrzenia może prowadzić do niskiej czystości produktu końcowego. Ważne jest również, aby monitorować proces na bieżąco i dostosowywać parametry w trakcie destylacji, co może pomóc w uniknięciu wielu problemów. Nie można zapominać o odpowiednim schładzaniu pary, ponieważ niewystarczające chłodzenie może prowadzić do strat materiałowych oraz obniżenia jakości uzyskiwanego produktu.
Jakie są nowoczesne technologie w destylacji rozpuszczalników
W ostatnich latach rozwój technologii w dziedzinie destylacji rozpuszczalników znacząco wpłynął na efektywność i jakość tego procesu. Nowoczesne aparaty destylacyjne wyposażone są w zaawansowane systemy sterowania, które umożliwiają precyzyjne monitorowanie i regulację parametrów procesu. Dzięki zastosowaniu technologii automatyzacji możliwe jest zdalne zarządzanie procesem destylacji, co zwiększa bezpieczeństwo i komfort pracy. Wprowadzenie inteligentnych algorytmów pozwala na optymalizację warunków pracy urządzeń, co przekłada się na wyższą wydajność oraz lepszą jakość uzyskiwanych produktów. Ponadto, rozwój materiałów stosowanych w konstrukcji aparatów destylacyjnych przyczynia się do zwiększenia ich trwałości oraz odporności na działanie agresywnych substancji chemicznych. Warto również wspomnieć o zastosowaniu technologii membranowych oraz ekstrakcji cieczy cieczą jako alternatywnych metod separacji, które mogą być bardziej efektywne w niektórych przypadkach niż tradycyjna destylacja.
Jakie są różnice między destylacją a innymi metodami separacji
Destylacja rozpuszczalników to jedna z wielu metod separacji składników mieszanin, ale różni się od innych technik pod względem zasady działania oraz zastosowania. Na przykład ekstrakcja cieczy cieczą polega na wykorzystaniu różnicy rozpuszczalności składników w dwóch niemieszających się cieczy, co pozwala na ich oddzielenie bez potrzeby podgrzewania. Ta metoda jest często stosowana w chemii organicznej do oczyszczania związków chemicznych i może być bardziej efektywna w przypadku substancji o bliskich temperaturach wrzenia. Inną popularną metodą jest chromatografia, która polega na separacji składników mieszaniny na podstawie ich różnej interakcji z fazą stacjonarną i ruchomą. Chromatografia jest szczególnie skuteczna w analizie skomplikowanych mieszanin i pozwala na uzyskanie bardzo wysokiej czystości produktów końcowych. W porównaniu do tych metod, destylacja ma swoje unikalne zalety, takie jak prostota wykonania oraz możliwość przetwarzania dużych ilości materiału jednocześnie.
Jakie są przyszłe kierunki rozwoju technologii destylacji rozpuszczalników
Przyszłość technologii destylacji rozpuszczalników wydaje się obiecująca dzięki ciągłemu postępowi naukowemu oraz innowacjom technologicznym. W miarę jak rośnie zapotrzebowanie na czystsze i bardziej efektywne metody produkcji, badacze poszukują nowych rozwiązań mających na celu poprawę wydajności procesów destylacyjnych. Jednym z kierunków rozwoju jest integracja procesów chemicznych z technologią destylacyjną, co pozwoli na jednoczesne przeprowadzanie reakcji chemicznych i separacji produktów w jednym etapie. Takie podejście może znacznie uprościć proces produkcji oraz zmniejszyć koszty operacyjne. Inwestycje w nowe materiały konstrukcyjne dla aparatów destylacyjnych również mogą przynieść korzyści, takie jak zwiększona odporność na korozję czy lepsza przewodność cieplna. Dodatkowo rozwój technologii cyfrowych i sztucznej inteligencji umożliwi jeszcze lepsze monitorowanie i optymalizację procesów przemysłowych, co przyczyni się do dalszego zwiększenia efektywności produkcji.
Jakie są kluczowe czynniki wpływające na efektywność destylacji rozpuszczalników
Efektywność procesu destylacji rozpuszczalników zależy od wielu czynników, które należy uwzględnić podczas planowania i przeprowadzania operacji. Przede wszystkim kluczową rolę odgrywa temperatura wrzenia poszczególnych składników mieszaniny; im większa różnica temperatur wrzenia, tym łatwiejsze będzie oddzielenie składników. Ważnym aspektem jest także ciśnienie atmosferyczne; obniżenie ciśnienia może zmniejszyć temperaturę wrzenia substancji, co ułatwia proces destylacji i może prowadzić do oszczędności energetycznych. Kolejnym czynnikiem wpływającym na efektywność jest powierzchnia kontaktu między parą a cieczą; zwiększenie tej powierzchni poprzez zastosowanie kolumn frakcyjnych lub innych zaawansowanych urządzeń może znacząco poprawić wyniki separacji. Należy również pamiętać o odpowiednim schładzaniu pary; skuteczne chłodzenie zapewnia lepszą kondensację pary i minimalizuje straty materiałowe.
Jakie są najważniejsze aspekty bezpieczeństwa podczas destylacji rozpuszczalników
Bezpieczeństwo podczas procesu destylacji rozpuszczalników jest kluczowym zagadnieniem zarówno w laboratoriach badawczych, jak i zakładach przemysłowych. Przede wszystkim należy zadbać o odpowiednią wentylację pomieszczeń roboczych; wiele rozpuszczalników jest lotnych i toksycznych, dlatego ważne jest unikanie ich nagromadzenia w powietrzu. Użytkownicy powinni być wyposażeni w odpowiednie środki ochrony osobistej, takie jak rękawice czy okulary ochronne, aby minimalizować ryzyko kontaktu ze szkodliwymi substancjami chemicznymi. Również właściwe zabezpieczenie sprzętu przed przegrzaniem czy uszkodzeniem mechanicznym ma kluczowe znaczenie dla zapewnienia bezpieczeństwa operacji; regularne przeglądy techniczne urządzeń powinny być standardową praktyką w każdym zakładzie zajmującym się destylacją. Warto również wdrożyć procedury awaryjne oraz szkolenia dla pracowników dotyczące postępowania w sytuacjach kryzysowych związanych z wyciekami czy pożarami związanymi z używanymi substancjami chemicznymi.